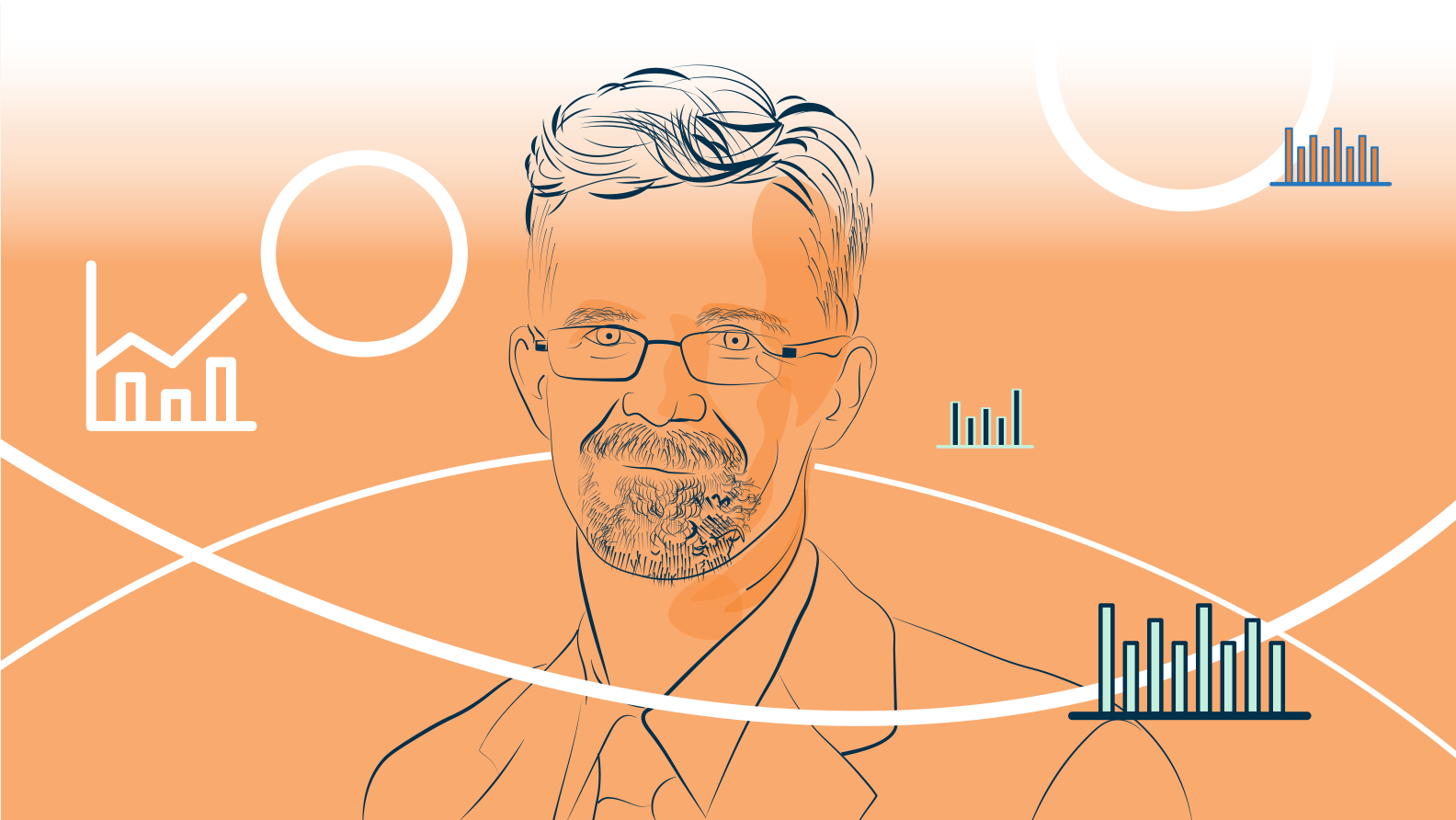
Analityka danych w przemyśle 4.0 — „nie wolno cyfryzować bałaganu”
— Jeżeli nie mamy zaufania do danych, a planujemy je wykorzystać do podejmowania decyzji, najprawdopodobniej otworzymy puszkę Pandory, co skończy się katastrofą — przestrzega Jarosław Smulski z IDC.
Jarosław Smulski pracuje jako Senior Program Manager w IDC Poland. Od wielu lat analizuje rynek IT, prowadzi zaawansowane badania wertykalne, segmentuje modele wydatków IT i tworzy opracowania typu go-to-market. Znajomość technologii wykorzystuje również w projektach doradczych. Oprócz tego upowszechnia wiedzę na temat nowych trendów i strategii, takich jak internet rzeczy, przemysł 4.0 czy smart city. Jest członkiem Grupy Roboczej ds. Internetu Rzeczy przy Kancelarii Prezesa Rady Ministrów.
Powiedziałby pan, że przemysł 4.0 już istnieje?
Wszystko zależy, czy rozmawiamy z polskimi firmami, czy międzynarodowymi korporacjami, które realizują w Polsce testowe rozwiązania, często dla całej organizacji. W drugim przypadku łatwiej o takie przeświadczenie, ponieważ przedsiębiorstwa te mają odpowiednie pieniądze i dostęp do wysokiej klasy specjalistów. Można powiedzieć, że te firmy są blisko realizacji celu, jakim jest przemysł 4.0.
A polskie firmy?
Niewątpliwe cyfryzacja mocno przyśpieszyła w trakcie pandemii, także w firmach produkcyjnych w naszym kraju. Nadal jednak polskie przedsiębiorstwa mają sporo do nadrobienia. Problem jest choćby taki, że produkcja stosunkowo późno zaczęła podlegać globalnemu procesowi cyfryzacji. Dlatego brakuje często zrozumienia, jakie korzyści przynoszą przemysłowi nowoczesne rozwiązania. Niestety dla wielu przedstawicieli branży produkcyjnej informatyka to nadal back office. Dział, który ma spełniać rolę służebną dla innych operacji i działań.
Czyli dziś jesteśmy bliżej przemysłu 3.5 niż 4.0?
Zdecydowanie tak, choć nie wykluczam tu jeszcze niższego poziomu w niektórych obszarach. Co prawda czasem słyszymy, że jesteśmy już w tej fazie 3.5, ale może chcemy być tak postrzegani? A tymczasem, jeśli popatrzymy na otaczającą nas rzeczywistość, jest ona mniej optymistyczna.
To może wynikać z konkretnych modeli biznesowych? Wiele branż nie widzi ograniczeń w tym zakresie.
Nie powiedziałbym, że to kwestia specyfiki jakiejś branży — już szybciej rozmiarów firmy i odpowiednich budżetów. Niezależnie, czy to będzie przemysł wydobywczy, czy spożywczy, wyzwania dla nich są mniej więcej zbliżone. Oczywiście każdy rodzaj produkcji ma swoją specyfikę. Jednak największym wyzwaniem w polskim przemyśle jest zrozumienie pilnej potrzeby digitalizacji. I to z uwzględnieniem strategii cyfrowego rozwoju produkcji, ale w oparciu o dane.
Dane są podstawą całego procesu cyfryzacji. Rozumiem, że pozostaje pytanie, jak je skutecznie wykorzystać w przemyśle?
Podstawowym problemem jest to, aby nie zdigitalizować i nie zinformatyzować bałaganu. A z takim mamy w wielu firmach do czynienia. W jednym z wywiadów w serwisie “Data Science robię” na temat smart city (“Dane jako paliwo dla rozwoju nowoczesnych miast”) pada stwierdzenie garbage in, garbage out. I w tym jednym haśle zawarte jest to, z czym borykają się dziś firmy przemysłowe w Polsce. Przedsiębiorstwa, które nie mają jeszcze w pełni opomiarowanych linii produkcyjnych, z reguły kupują sprzęt, np. sensory IoT, które można łatwo podłączyć do sieci i w ten sposób zbierać dane. Niestety problemem jest ogromna silosowość informacji, technologiczny bałagan, różne formaty zapisu. Dlatego okiełznanie tej stajni Augiasza może być kolejnym potężnym wyzwaniem dla firm produkcyjnych. W przeciwnym razie nie będzie możliwe zrobienie następnego kroku, czyli stworzenie tzw. data lake’ów, czyli przestrzeni, gdzie dane, pochodzące z różnych źródeł, są w miarę ustandaryzowane. A to warunek dla powstawania i uczenia modeli AI, które chcielibyśmy wykorzystywać do podejmowania decyzji biznesowych opartych na danych.
W przemyśle wiele danych pozyskiwanych jest bezpośrednio z linii produkcyjnej. Ale inaczej jest już w branży finansowej. Jakie to ma znaczenie?
Zdecydowanie czym innym jest analizowanie danych, które są od dekad zbierane przez systemy informatyczne, a czym innym jest otwieranie się na dane, które dopiero zaczynamy zbierać. Dlatego dodawanie do systemu danych bezpośrednio z produkcji może generować dla firm poważne problemy. Tym bardziej że w przemyśle mamy do czynienia z rozdzieleniem świata automatyki od IT. Powodem takiego stanu rzeczy bywa czasem kwestia bezpieczeństwa czy kultury korporacyjnej. Co więcej, dziś wiele firm nadal analizuje dane rozłącznie, a dopiero później łączy je za pośrednictwem jednego interfejsu. Pozostaje kwestia, jak długo jesteśmy w stanie utrzymać podobny model. Natomiast firmy, które scalają automatykę przemysłową i informatykę, przynajmniej próbują zasysać te dane z operacji i produkcji do systemów analitycznych. Pełna analiza danych ze wszystkich źródeł jest niezbędna dla budowy modeli tzw. bliźniaków cyfrowych. Niestety w tej chwili niewiele korporacji jest gotowych, żeby wprowadzać pełną digitalizację całego procesu produkcyjnego, bo wiąże się to z analizą ogromnej liczby danych. A tylko pełne odzwierciedlenie tych wszystkich procesów, które istnieją w firmie, pozwala w pełni wykorzystać zalety digital twin.
Jak zatem firmy podchodzą dziś do analizowania swoich danych?
Z jednej strony możemy zasysać te dane, które mamy, chociażby z linii produkcyjnej czy maszyn i na ich podstawie opracowywać określone modele. Taka analityka predykcyjna jest prosta do zobrazowania dla działów operacyjnych firmy. Umożliwia wykazanie szybkiego zwrotu z inwestycji. Jeśli wiemy, ile kosztuje nas awaria danej maszyny czy linii produkcyjnej, uniknięcie jej pozwala nam zaoszczędzić określoną sumę pieniędzy. To tzw. wyspowe podejście, bardzo pragmatyczne, które pozwala obniżać koszty, np. ograniczyć zużycie prądu w trakcie produkcji. Mamy w konsekwencji optymalizację, ale ta nie przekłada się na pełną digitalizację działania firmy. Czymś innym jest analiza danych. Jej wartość była doskonale widoczna podczas zarządzania procesami w momencie zawirowań w łańcuchach dostaw, z którymi mieliśmy do czynienia w trakcie i po pandemii, a także w momencie wybuchu konfliktu w Ukrainie. Wtedy analiza danych stała się bardzo istotna dla przemysłu. Wiele firm produkcyjnych zaczęło zwracać na to baczną uwagę, doinwestowywało działy, które odpowiadają za analizę danych czy zaczęło korzystać z odpowiednich rozwiązań.
Co z wykorzystaniem sztucznej inteligencji?
Po to robimy procesy konsolidacji, czyszczenia, zbierania informacji, aby w pewnym momencie użyć algorytmów, które będą wyławiały pewne schematy. Stworzyć system samouczący, który umożliwi podejmowanie lepszych decyzji, to jest zakładana strategia chyba w każdym tego typu modelu. Przemysł nie ucieka od sztucznej inteligencji. Zbieranie danych wyłącznie po to, aby je posiadać, nie ma żadnego sensu. To następny krok, jeden z wielu, kiedy mamy wdrożoną strategię transformacji cyfrowej. Niestety, jeśli wprowadzamy zmiany ad hoc, bez odpowiedniego przygotowania, wszystko jest chaotyczne. Wtedy nie unikniemy błędów, silosów danych i cały proces migracji do cyfrowego modelu będzie bardzo utrudniony. A w takim scenariuszu użycie sztucznej inteligencji może przynieść więcej kosztów niż zysków.
Dwa żywioły — biznes i IT — da się pogodzić?
Problemem jest kwestia, kto tak naprawdę jest posiadaczem danych z punktu widzenia procesów biznesowych. Czy już IT, czy w dalszym ciągu działy operacyjne? Jeżeli IT, to jest większa szansa, że zostaną one wyczyszczone i uporządkowane. Natomiast jeśli dane będą nadal w działach biznesowych, w zasadzie będzie to wiązało się z bezczynnością. Powiedzmy sobie prawdę, działy operacyjne nawet nie dotykają pewnych systemów działających w firmie, z powodu braku wiedzy. W wielu fabrykach jest tak, że tzw. wiedza instytucjonalna odchodzi z ostatnim pracownikiem, który tworzył konkretny system.
Mamy więc szereg wyzwań dla przemysłu. Pandemia pokazała potrzebę lepszego zarządzania procesami oraz to, że przemysł 4.0 jest naprawdę potrzebny.
Trzeba przede wszystkim zrozumieć, że przemysł 4.0 to nie są komputery, serwery czy systemy ERP. Należy zmienić podejście na data driven business. Podejmujemy decyzję w oparciu o dane, następnym krokiem jest automatyzowanie procesów podejmowania decyzji po to, aby wyeliminować czynnik ludzki tam, gdzie on jest zbyteczny. Niezbędne są też modele, w których decyzje podejmują algorytmy, a człowiek tylko nadzoruje, czy wszystko idzie we właściwym kierunku. Dlatego tak istotne jest, aby dane były rzeczywiście wiarygodne, całościowe, aby eliminować zafałszowania, co dotyczy też danych zbieranych przez sensory. Jeżeli nie mamy zaufania do danych, a planujemy je wykorzystać do podejmowania decyzji, otworzymy puszkę Pandory i w efekcie może dojść do katastrofy.
W jakim stopniu jesteśmy w stanie zaufać procesowi zbierania danych? Przecież wystarczy, że jakaś liczba sensorów IoT straci zasilanie i już otrzymujemy całkowicie inny odczyt danych.
Jeżeli się nie zorientujemy i nie mamy systemu zarządzania tymi sensorami, który będzie sprawdzał na bieżąco wszelkie awarie czy wyczerpanie baterii, to dane, które będziemy zbierali dadzą nam całkowicie fałszywy obraz sytuacji. Co z tego, że nasze decyzje w oparciu o dane będą prawidłowe z punktu widzenia logiki działania algorytmu, skoro będą całkowicie błędne, ponieważ nie odzwierciedlą rzeczywistości? Jeżeli natomiast zabraknie systemu do zarządzania bezpieczeństwem IoT, może to doprowadzić do poważnego zagrożenia dla działania całej firmy.
Wskazuje Pan na poważne ryzyka związane z zaufaniem do technologii. To zagrożenie dla cyfryzacji sektora produkcyjnego?
Generalnie ludzi z przemysłu charakteryzuje bardzo daleko posunięty pragmatyzm i konserwatywne podejście do nowinek technicznych. Wynika to z faktu, że błędy mogą przekładać się na ogromne straty. Nie mówiąc już o zagrożeniach dla bezpieczeństwa pracowników a nawet dla bezpieczeństwa strategicznego państwa. Nie spodziewam się, że firmy zaczną podejmować pochopne decyzje czy decydować się na drogę na skróty lub podejmowanie ryzykownych działań. Proszę pamiętać, że w przemyśle, w firmach produkcyjnych wszystko podlega drobiazgowym audytom. Dodatkowo, sektor przemysłowy dosyć chętnie korzysta z usług zewnętrznych konsultantów i ich wiedzy. Decyzje o informatyzacji procesów są i będą podejmowane racjonalnie.
Mówiliśmy sporo o problemach. A jakie pan widzi wyzwania dla tej branży związane z procesami cyfryzacyjnymi?
Fundamentalna jest kwestia, jak obecnie działające technologie wykorzystać skutecznie w przemyśle. Nie ma wątpliwości, że problemem jest dostępność na rynku odpowiednich specjalistów. Mówię o analitykach, o data scientistach. Trzeba zdecydować, czy nasze dane będziemy przetwarzać u siebie, czy w chmurze. Czy jesteśmy wystarczająco dużą organizacją, aby budować własne działy analityki danych? W jaki sposób ułożyć współpracę między biznesem i IT?
I jak firmy podejdą do tych wyzwań?
Przemysł jest dobrze zarządzany. Wszelkie strategie, które zostały wprowadzone do tej pory, poddano intensywnym stress testom w momencie pandemii. Powtarzam często hasło, którego autorem jest Tomasz Haiduk (wieloletni manager w Siemensie, prezes Forum Automatyki i Robotyki Polskiej – red.), że w produkcji skończyły się czasy księgowych, a zaczęły czasy ludzi, którzy zajmują się zawodowo ryzykiem. Dziś bezpieczeństwo w przemyśle to nie tylko cyberbezpieczeństwo, ale przede wszystkim bezpieczeństwo procesów zarządzania produkcją, bezpieczeństwo danych, czy choćby to finansowe. Dlatego szczególnie ważne jest wdrażanie w tych obszarach strategii cyfrowej odporności. Wydaje mi się, że jeśli firmy będą czerpały z podobnych wzorców, mamy dobry przepis, aby uniknąć podejmowania zbyt ryzykownych decyzji. Gwałtownie rosnąca ilość projektów pozwala nam jednak z pewnym optymizmem patrzeć w przyszłość. Wierzę, że procesy budowy cyfrowych modeli zarządzania produkcją będą powstawały w najbliższym czasie w szybkim tempie, co przełoży się nie tylko na dalszą optymalizację procesów produkcji, ale również poprawi odporność całych łańcuchów wartości w gospodarce.